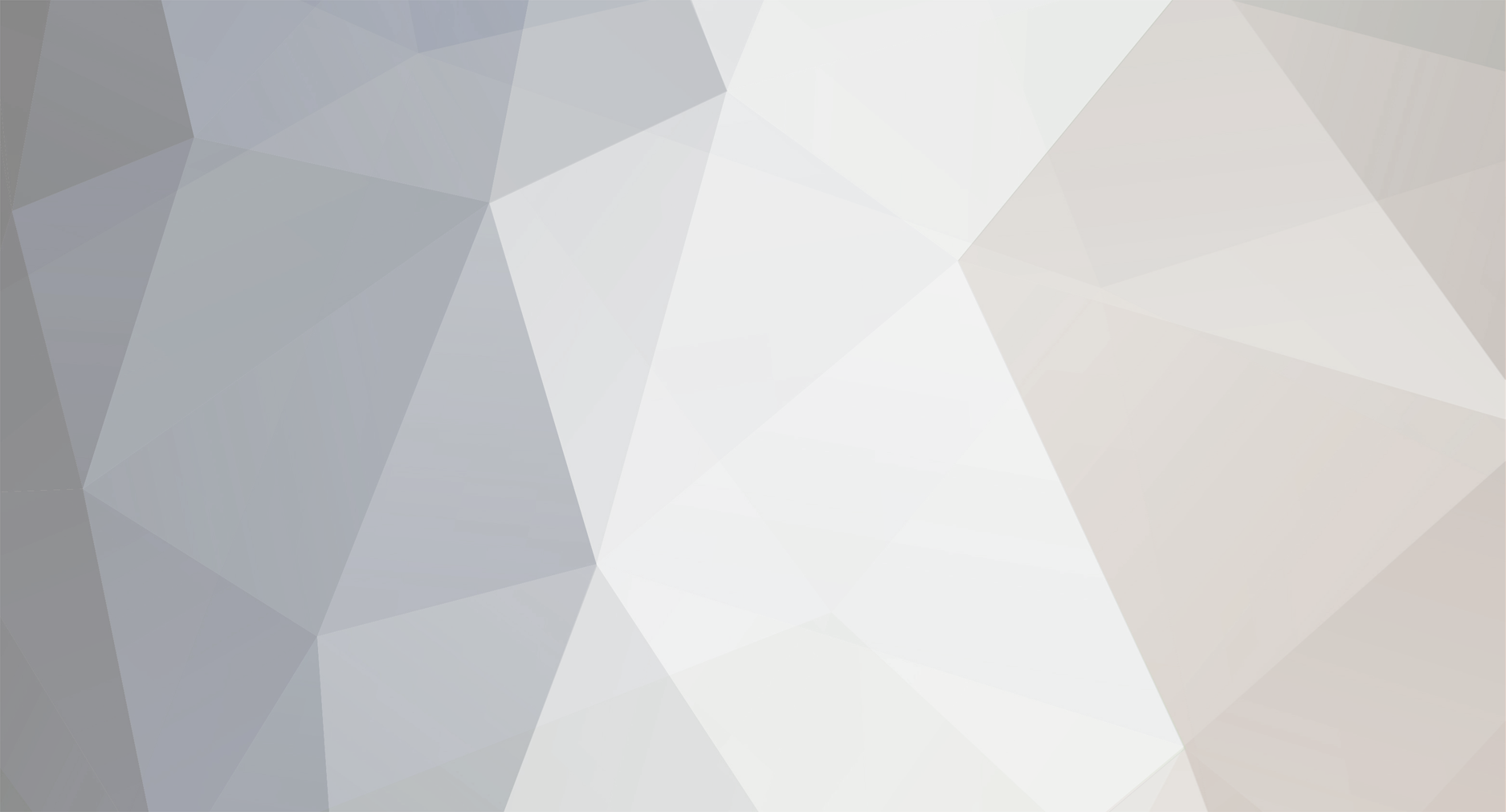
indulis
-
Posts
488 -
Joined
-
Last visited
Content Type
Profiles
Forums
Events
Posts posted by indulis
-
-
Yes... but there is no "C" here. It's a series RL circuit.
You short windings of a transformer to measure leakage inductance, but the transformer isn't active. To measure the leakage inductance of a winding, short ALL other windings and measure the L of the winding of interest on a bridge at the frequency the transformer operates... repeat for each winding. I don't see how shorting a winding will help you find copper loss. You need to know either the RMS voltage or current across the winding to do that. To take into consideration higher order affects, the temperature is needed as well as it can/will change the resistance. -
You were doing what?? You can't connect a wire across a transformer winding... that is a short. Yes, a transformer will get hot if you short it's winding.
Tell us a bit more about...... find the resonance frequency of a copper wire.
Resonance with what? Self resonance? How are you changing the frequency? At best wire "looks like" a series RL... wire is about 20nH/inch and the wire resistance is very small. You could calculate the frequence where XL=R -
Yes... DC-DC converters will do what you want. The power range your looking at is NO PROBLEM!!
-
The motherboard.
There are electronics someplace that control the "power-up" sequence and type. Are you trying to margin test the voltage, or the sequence time? -
It's not the sequence of the power supplies themselves that is important, but it could be VERY important to what they are "powering-up". For example, some CPU's are very particular in what order it see's which voltage.
-
The DC source does not matter... whether it's a battery or rectified AC.
-
You could use something called a buck-boost converter.
-
Frequency does matter.
In a power application for example... take a simple buck converter, Vout/Vin will tell you the ~ duty cycle, but the frequency will determine the "off time" (flywheel period during which current is flowing out of the inductor) of the converter. That "off time" plays a role in the inductor value and will determine the ripple current amplitude. A properly sized "power inductor" that works at 100KHz will not work at 1KHz... it will saturate. Frequency will determine max flux excursion and hence, max current capability. -
In your schematic you show pins 12 & 13 connected to the drain of the the IFR 540. This is a switching node (the voltage goes up and down and you don't want that). They (pins 12 & 13) should be connected to either Vin or the Vref pin and you need a pull down resistor on the driver input.
First, you can't do current control with this PWM. To do "average" current mode control you will need to sum the high side FET's current information with the flywheel current information and send that back to the PWM (current mode) ramp pin.
Check out
http://focus.ti.com/lit/ml/slup091/slup091.pdf
There are a ton of PWM's from Linear
http://www.linear.com/pc/viewCategory.do?navId=H0,C1,C1003,C1042
but their site seems to be having problems right now, so I can't look one up.
How much output current do you want? It will matter for your inductor value and the output cap ESR!! 50mV of ripple at a 1A output is VERY different from 50mV of ripple at 10A!! -
John, John, John
-
In "your" circuit, you have pins 12 & 13 tied to the drain of the MOSFET... I think they should be tied to either Vref or to Vin unless in your final design the Vin voltage will be to high for MOSTFET driver.
While you could use this voltage mode control PWM (SG3524), it's considered "old" in the industryand there are better PWM's out there that are specifically made for Buck converters (for both synchronous and non-synchronous configurations) and won't need a driver IC, as bootstrap circuitry is onboard for driving high side FET's.
Can you tell us a little more about your design?? i.e. input voltage, output voltage, switching frequency, expected ripple current, output ripple voltage and since this is a voltage mode controller the minimum load current (this will directly impact the inductor value)... etc.
Your IRF540 is big time overkill for a 15V input voltage... is it needed or is it something you just happen to have on hand? -
Audioguru
First you saidA 3.3V zener diode doesn't regulate very well. A 6.8V zener diode regulates 11.5 times better...
Then you brought "dynamic impedance " into the picture for some reason (NEVER applied to this circuit) and now your saying...The zener diode isn't regulating anything because the input voltage is regulated...
If the zener isn't regulating anything, then what is controlling the output voltage??? Whether the load is changing or not in this circuit is irrelevant. The point was that because the input voltage was regulated and the typical Hfe of a small signal transitor is high enough to not affect the the current in the zener current limit resistor, ergo no dynamic behavior!!!!
-
Audioguru
While you didn't exactly answer the question directly, your reply kinda has the answer if you "read between the lines". OK, now let gets back to why you think "dynamic impedance " comes into play in this particular circuit, as in your reply, you basically stated that the circuit DOESN'T have "any" (virtually non-existent) dynamic properties? Now if the regulated 5V feeding the circuit wasn't so regulated... that would be a different story as there would now be some "dynamic" circuit behavior.
I misspoke earlier in regards to not using the series diode with zeners below 5.1V. The diode also does a "good" thing!! The diode in series with the zener diode has the effect of cancelling changes due to Vbe changes with temperature. -
ou could use a buck converter. Limiting the current for the 5V @ 1-2A could be an issue if you can't live with a fuse.
-
The amount of current and frequency has a lot to do with selecting the proper core shape (for cross sectional area) and material (for Bsat). How much ripple current can yo live with?
For example, you won't use toroid at very high frequencies because of the losses.
You can get toriods in soft ferrite material now and the "Cool-Mu" toriods from Magnetics work very well in SMPS. -
Audioguru
Before I reply, please give me your definition of “static and dynamic” circuit behavior, and into which catagory you feel this particular circiut falls. Again, the 3.3V is being derived from a regulated 5V. -
This is a static type application (regulated 5V to 3.3V), so exactly how does a 6.8V zener regulate 11.5 times better than 3.3V zener? Please explain why you think "dynamic impedance " comes into consideration here?
The magic number is 5.1V for a zero temperature coefficient. The series diode in this case hurts regulation as both zener and diode forward voltage are both going down... use the series diode when the zener has a positve temperature coefficient (i.e. >5.1V). -
I would think more like 400Hz (F=1/(5*.5ms).
-
In your simulation, the M6 gate signal is referenced to gnd. The only thing that matters is Vgs, so you have to use the M6 source as a reference when looking at whats going on at it's gate.
...I cant get decent PNP Mosfets...
PNP MOSFET's?? Do you mean P channel?
Electric golf carts use regenerative braking for "braking" and putting power back into the battery, not motor speed control. Shaft encoders are the general choice for speed control... you don't drive your car with one foot either on the gas or the brake at all times, why would you want to do it with a DC motor? -
Hmmmm...
If M7 is on all the time and you turn on M5, you are shorting the motor... is this what you wanted? There also doesn't appear to be a "flywheel" device across the motor. You could put a clamp zener on the gates to "limit" the spike or you could try snubbers across M6 & M5. Have you ever looked at this site...
http://www.4qdtec.com/pwm-01.html
some interesting stuff there!! -
-
... if I'm applying a high frequency that may cause excessive phase shift...
Applying a high frequency signal to an opamp circuit doesn't change the circuits phase shift. Opamp "compensation circuits" change/alter the gain/bandwidth of the circuit and is fixed... the poles and zeros that the compensation circuit introduces don't move around just because you change the frequency of the input signal.
The transfer function of Audioguru's circuit is -
It is a flyback converter. The secondary, with the polarity as shown will go negative to the collector of the transistor. The resistor is used to turn off the transistor when the breaker opens. It value isn't critical, but you can waste a lot of power if you make it's value to low.
-
That formula isn't "exactly" true. To keep the math simple, consider i=C*dv/dt. Rearrange the terms... (i*t)/C=dv This tells you that for a given capacitor of value "C", drawing "i" amps for "t" seconds will result in a voltage dip of "dv". If a square wave was charging the capacitor, the calculation is simple, the capacitor is either being charged, or discharged. With a full wave rectified sinusoid the calculation becomes quite a bit more complicated, as it's not either one state or the other. The "dt" time suggested in the calulation of 1/(2*60) is the "entire period" which isn't accurate. Plus, higher order affects, such as ESR, aren't taken into account. It's easy to see that if you had a ESR of 1 ohm at 120Hz (ESR is frequency dependent), a 24 amp load by itself will cause a 24V dip.
Help me choose a mosfet
in Power Electronics
Posted
Take a look here
http://www.vishay.com/mosfets/lteq-20-v/micro-foot-package/
Note the Rds on with a Vgs of only 1.5V!! Even at 2.5V they are all below .05 ohms
In general, you'll find that N channel MOSFET's have lower Rds on numbers than P channel.