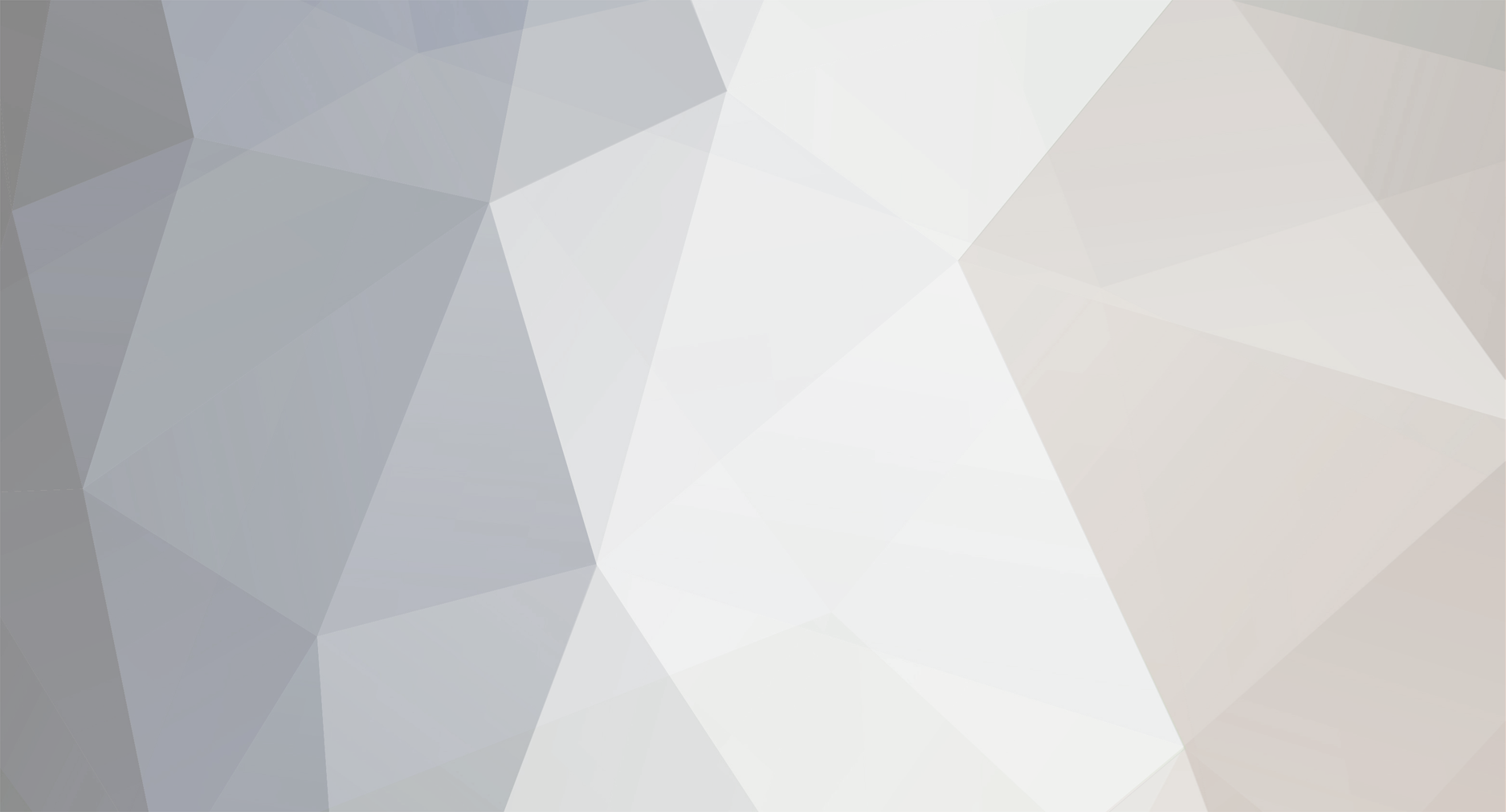
AN920
Members-
Posts
359 -
Joined
-
Last visited
Never
Content Type
Profiles
Forums
Events
Everything posted by AN920
-
Duty Cycle control for square wave inverter
AN920 posted a topic in Electronic Projects Design/Ideas
It appears that a lot of members are interested in building simple square wave inverters from diagrams on this forum. Problems with these designs are that the drive wave to the push pull transistors or fets does not have any dead-time or duty-cycle control. Dead time makes sure one side is turned off before the other side turn on. This is important when operating near maximum duty cycle. Also by varying the duty we can to some extent control the final output voltage of the inverter as this is set by : Vin x transformer ratio x duty (or on time) My design provides the frequency as well as the duty cycle to be set using standard CMOS parts. R2 set the output frequency from about 45-65Hz. R1 can set the duty cycle between about 5-95% although it will never be used that low. The added advantage is that with this control circuit you can now use a transformer with lower primary voltages like 6+6 or 9+9 while still using the standard 12V source. The correct Vsec is maintained by adjusting the on time. -
I touched on this subject in another post. Here the basic information to do such a modification. The diagram shows the basic blocks of a squarewave inverter with the two resonating elements (C1, L1) added. The values are load dependant and the values shown works for a 100W load. In the first case C1, L1 is switched in circuit producing the waveforms shown. When C1,L1 is taken out by switch S1 the typical squarewave switching waveform returns. Note that C1 should be non-polarized and L1 should be capable of carring the switching current without saturating. Average values can be calculated by this: Xc = E^2/(10^3 x 1.5 x kVA) where kVA is the rated kVA load on the output C = 10^6/(2 x Pi x f x Xc) L = 10^6/[4 x (2 x Pi x f)^2 x C] EC = 2.5 x DC in
-
Inverter Circuit 12V DC to 230VAC Sine Wave
AN920 replied to harrychoo's topic in Electronic Projects Design/Ideas
A square wave inverter can provide a reasonable sine wave output with a few modifications. This was a common method long ago before fast switching pwm. This was implemented with scr type square wave inverters but can also be applied to transistor or fet types. Basically the switching current is forced to be resonant producing a sine output. This was good up to several kW's. The drawback is that the tuning element values are somewhat load dependant. Also voltage regulation is also load dependant. A more complicated sceme can be used which requires a extra tap on each half secondary winding to provide passive feedback to overcome these problems. Performance was typical 2.5% output change for 25% input variation at full load. Pictures show typical waves to be expected from this inverter. One is from my simulation and other from actual documented test. -
Why is so hard to mimic the Knight Rider scanner Effect?
AN920 replied to wuemura's topic in Projects Q/A
Just leave out the top and bottom leds making it 8 in total -
Why is so hard to mimic the Knight Rider scanner Effect?
AN920 replied to wuemura's topic in Projects Q/A
Possible analog version. RV1 sets amount of smear. RV2 full scale cal. RV3 set the sweep rate. -
Why is so hard to mimic the Knight Rider scanner Effect?
AN920 replied to wuemura's topic in Projects Q/A
If you use the zoom tool you can see it clearly. Here is GIF version. I added a screen capture small AVI file of the simulated led movement. It looks a bit jerky because I think my PC is running out of computing speed running the simulation and the capture software but it will give some idea of the operation. -
Why is so hard to mimic the Knight Rider scanner Effect?
AN920 replied to wuemura's topic in Projects Q/A
Here is my digital design that includes the smearing effect. The pot sets the sweep rate. I have not tested the circuit in real life but it simulates well. -
Why is so hard to mimic the Knight Rider scanner Effect?
AN920 replied to wuemura's topic in Projects Q/A
You can create the optical illusion of smearing by using dither with the leds. This can be done in analog or digital -
It works because of the residual magnetism remaining in the motor without the need for any external excitation.
-
If you take an induction motor and drive it faster than it synchronous speed it becomes a generator or also called a "asynchronous generator" To use this as a generator without any external AC source you need something to supply the reactive power. This can be done by capacitive loading.
-
fm transmitter scematic required
AN920 replied to maxparveen's topic in Electronic Projects Design/Ideas
I must agree with you that I have never seen any worthwhile specifications published by Ramsey on their transmitters! Maybe because the final outcome relies on the builder builing it correct. But then they can do it for the export- fully assembled models. -
fm transmitter scematic required
AN920 replied to maxparveen's topic in Electronic Projects Design/Ideas
Have you tried any of the other stock names like Ramsey before? -
fm transmitter scematic required
AN920 replied to maxparveen's topic in Electronic Projects Design/Ideas
Sounds very promising. Please report again once you finished testing with your new antenna. BTW what other transmitters can you compare the unit against? Can you say which types you tried out before? -
fm transmitter scematic required
AN920 replied to maxparveen's topic in Electronic Projects Design/Ideas
Was wondering if you could give us a report when you receive this transmitter? -
Newbie needs help with a project
AN920 replied to DzlJim's topic in Electronic Projects Design/Ideas
Here is a modification to prevent the on-time from exceeding the clock period if the clock rate is made faster. This will prevent 2 injectors to be on at the same time. -
Newbie needs help with a project
AN920 replied to DzlJim's topic in Electronic Projects Design/Ideas
Here is your basic circuit. R4 adjust the firing rate per minute. R2 adjust the time the pulse will be high. The pulse out will drive a FET to switch the injectors. R5 will determine the minimum on time of the pulse. R6 will set the maximum clock rate. From the pictures: top trace is clock, next is the (1 of 4) counter outputs to the monostables. Only 1 monostable shown. You will have to duplicate 3 (the 4013 section and parts D1, R5,C1,R2) more. Bottom trace shows the output pulse from the monostable. You can see how the firing rate and pulse width changes with adjustment of the pots. One will have to select the values so that the max on time of each monostable is shorter that 1 period of the clocks signal so only 1 injector fires at a time-fixed in last mod C2 can be shorted and R3 removed, just I have a habit to provide short reset pulses which makes debugging more complex circuits easier. You will find all these parts at www.digikey.com -
Newbie needs help with a project
AN920 replied to DzlJim's topic in Electronic Projects Design/Ideas
Use a 4 stage counter driven by a clock. Use the counter outputs to trigger 4 separate monostables. The time constant from the monostable can be varied with a pot. Each monostable can fire a power fet to switch the injectors. The clock could also be varied with a pot. This is the idea, now remaining are the details. Think 555 clock, 4017, counter, 4013 monostables etc.. -
Those values are not critical. As long as you get the same adjustment voltage range on the pot without too much current through the pot you will be ok. You should always pick your values to have very little dissipation in the pot by limiting the current flow through the slider. I just noticed something; LED next to D6 should have a current limit resistor (~1k) in series otherwise it will blow when 12V is switched accross it. :o
-
You would expect the output of the opamp under ideal conditions to switch between supply and GND. Using a rail-to-rail opamp will bring you close to this. Older opamps can't switch like this. So if the low of your opamp switch to 0.4V the transistor may not be completely off. If the transistor operates in a high ambient temperature the b-e voltage threshold will be lowered at -2.5mV/degC By adding the extra diode drop you make sure that the transistor is off with 0.4V coming from the opamp.
-
The 1k resistors are to make sure enough current is available into the base to saturate T1. The diode is added because the opamp is not a rail-to-rail opamp and may not switch low enough to completely turn off T1. The added drop over D5 gives more switch off margin.
-
There are many chips available for this application. They will include all the special features like start boost, braking, reverse etc. which will be complex doing it with analog methods.
-
want to convert preamp from VHF 2 FM
AN920 replied to jaya000's topic in Electronic Projects Design/Ideas
Analyzing something like this normally involves smith charts and lots of complicated calculations. It may be difficult for someone to fully explore on this board. -
fm transmitter scematic required
AN920 replied to maxparveen's topic in Electronic Projects Design/Ideas
I stumbled onto the EDM page while looking for info on the BH chips. I never bought one as I made my own circuit with a BH1417. I looked at their mod meter at one stage and was thinking of getting one but found a surplus meter on ebay. I have seen a lot of post on the EDM transmitter on various boards. Looks like a good tranmitter. You may want to read the reviews on part15us. This is a site dedicated to low power transmitters AM& FM http://www.part15.us/node/691 There is something on the EDM as well -
fm transmitter scematic required
AN920 replied to maxparveen's topic in Electronic Projects Design/Ideas
The output of the Micromitter without the attenuator will be about 0.1mW and not 10mW -
NEED HELP IN A BAD WAY.... LED PROJECT
AN920 replied to telephoneman's topic in Electronic Projects Design/Ideas
You can do it many ways, some less elegant than others.