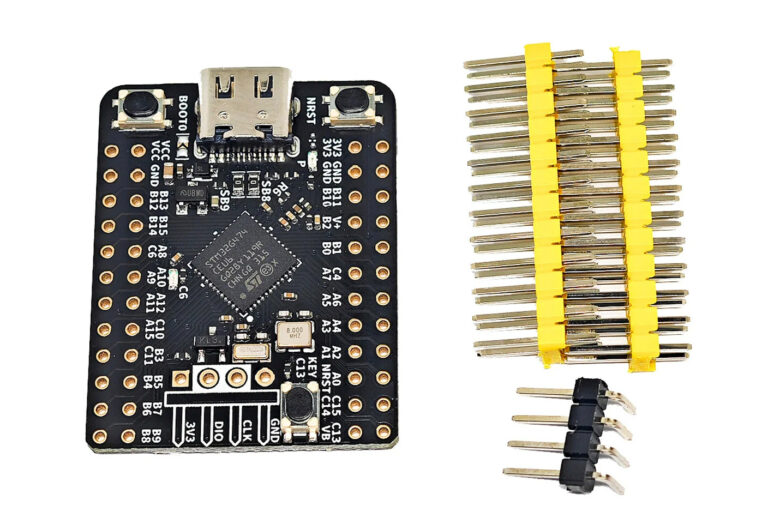
Introducing WeAct STM32G4: Tiny Development Board with Versatile Microcontroller Options
The WeAct STM32G4 is a compact development board that utilizes the STMicro STM32G4 Arm Cortex-M4F mixed-signal microcontroller. This microcontroller operates at a clock speed of 170 MHz and comes equipped with DSP (Digital Signal Processing) instructions, making it suitable for a wide...
Continue Reading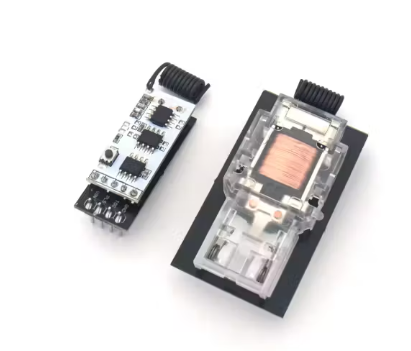
Questwise Ventures Introduces Energy-Harvesting Wireless Transmitter/Receiver for IoT Connectivity
Los Gatos-based Questwise Ventures has launched a new gadget that aims to deliver Internet of Things (IoT) connectivity without the need to power the transmitting side — by using an energy-harvesting push-button capable of driving its radio. Questwise Ventures, based in Los Gatos,...
Continue Reading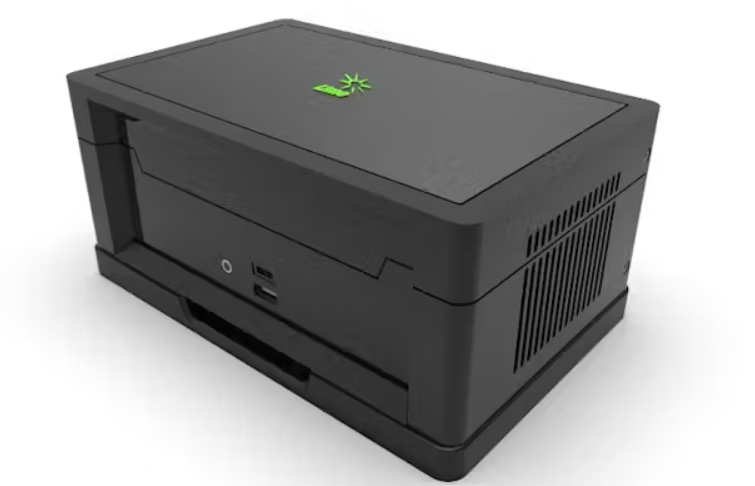
Vodafone and Lime Microsystems Unveil Upgraded 5G Network-in-a-Box with Raspberry Pi 5 Integration
Cellular network giant Vodafone and software-defined radio specialist Lime Microsystems have announced they will be showing off a revamped version of their 5G network-in-a-box device, built around a Raspberry Pi 5 single-board computer. Vodafone and Lime Microsystems have collaborated...
Continue Reading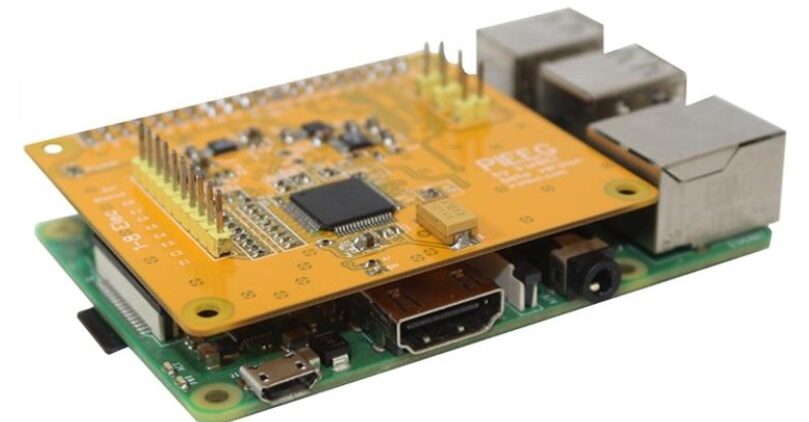
PiEEG A Raspberry Pi Shield for Measuring Biosignals like ECG, EMG, and EEG, Available for Just $350
PiEEG is an 8-channel, open-source shield for Raspberry Pi, designed to easily measure EEG, EMG, and ECG biosignals. It's user-friendly and compatible with various electrodes, making it easy to explore complex biosignals without needing specialized equipment. Researchers at Heriot-Watt...
Continue Reading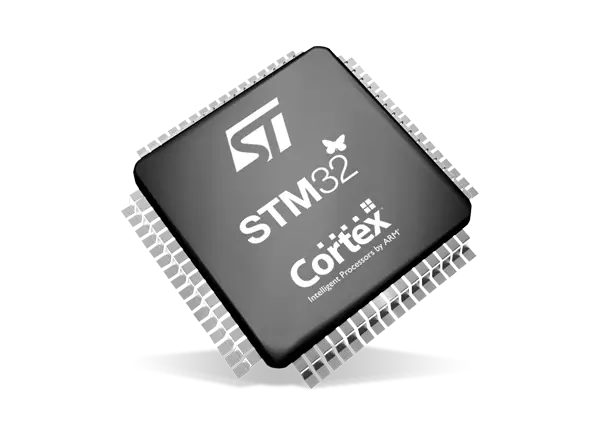
STMicroelectronics reveals advanced ultra-low-power STM32 microcontrollers
New flagship in ultra-low-power consumes less, delivers more at effective cost STMicroelectronics has introduced a new generation of energy-conscious and cost-effective microcontrollers (MCUs) that can reduce energy consumption by up to 50% compared to previous product generations....
Continue Reading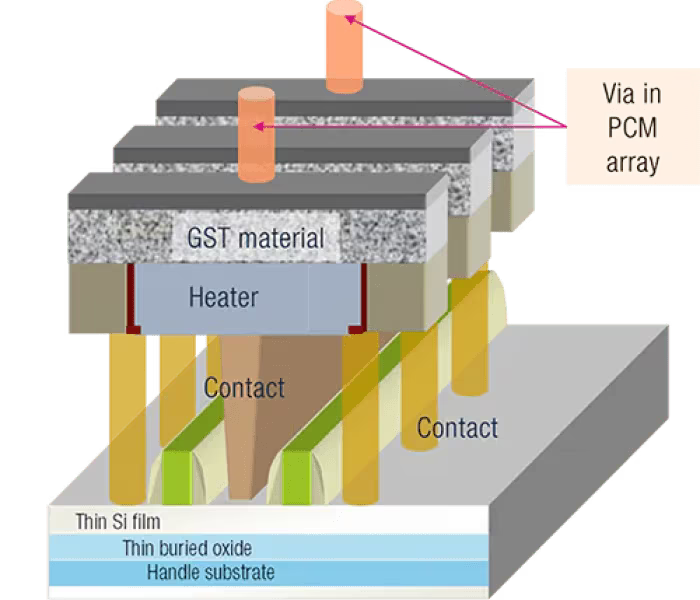
STMicroelectronics breaks the 20nm barrier for cost-competitive next-generation microcontrollers
Highlights First STM32 microcontroller based on new technology to sample to selected customers in the second half of 2024. 18nm FD-SOI with embedded phase change memory (ePCM) to deliver a leap in performance and power consumption. STMicroelectronics announces an advanced...
Continue Reading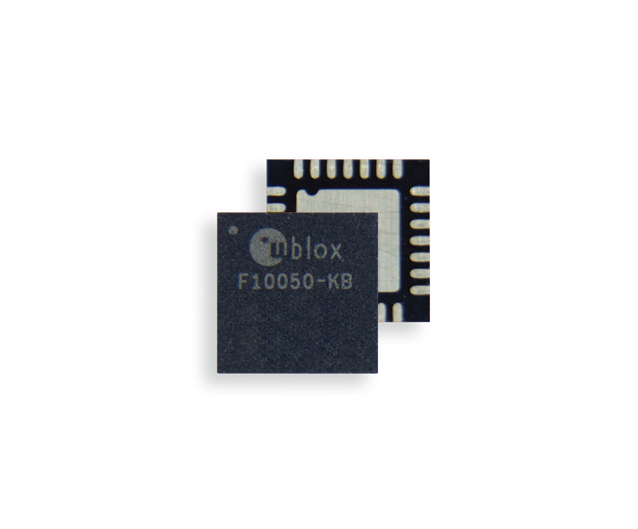
u-blox launches new GNSS platform for enhanced positioning accuracy in urban environments
The u-blox F10 platform increases positioning accuracy by reducing multipath effects, simplifying the process of promptly locating a vehicle. u-blox, a global provider of leading positioning and wireless communication technologies and services, has announced F10, the company’s first...
Continue Reading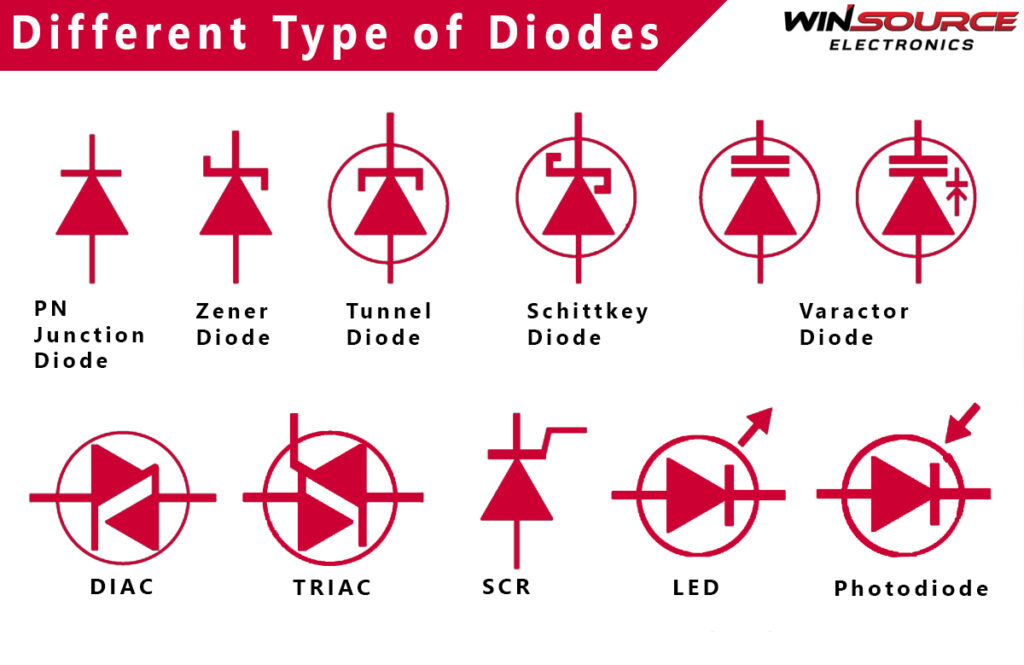
Choosing the Right Diode – Types and Uses Explained for Beginners
From small LED drivers to rectifiers to Switch Mode Power Supplies (SMPS), the diode is a key component in each of those everyday appliances. They are also used in charging LED indicators and reverse polarity protection circuits in router chargers and many more; diodes are used...
Continue Reading