
BeagleBoard’s New BeagleY-AI SBC Features Texas Instruments AM67A SoC with 4 TOPS Edge AI Accelerator
The BeagleBoard.org Foundation has recently released BeagleY-AI a Texas Instruments AM67A SoC powered SBC which promises open-source hardware in a standard form factor. The AM67A SoC features a quad-core Arm Cortex-A53 CPU, and dual DSPs with Matrix Multiply Accelerator, achieving a...
Continue Reading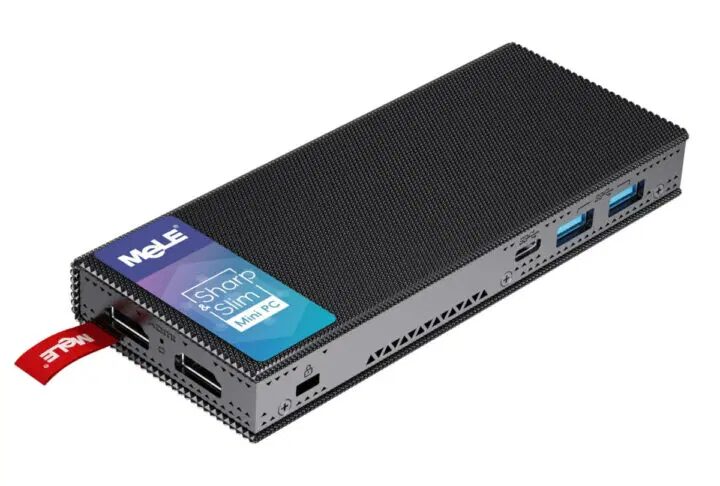
MeLE PCG02 Pro Gets Intel Processor N100 Upgrade: Fanless Mini PC Stick Enhanced
The MeLE PCG02 Pro, known for its ultra-slim and fanless design, has received an upgrade with the latest Intel Processor N100 Alder Lake-N CPU. Initially introduced with an Intel Celeron J4125 (Gemini Lake Refresh) or Celeron N5105 (Jasper Lake) processor in 2022, the PC stick now...
Continue Reading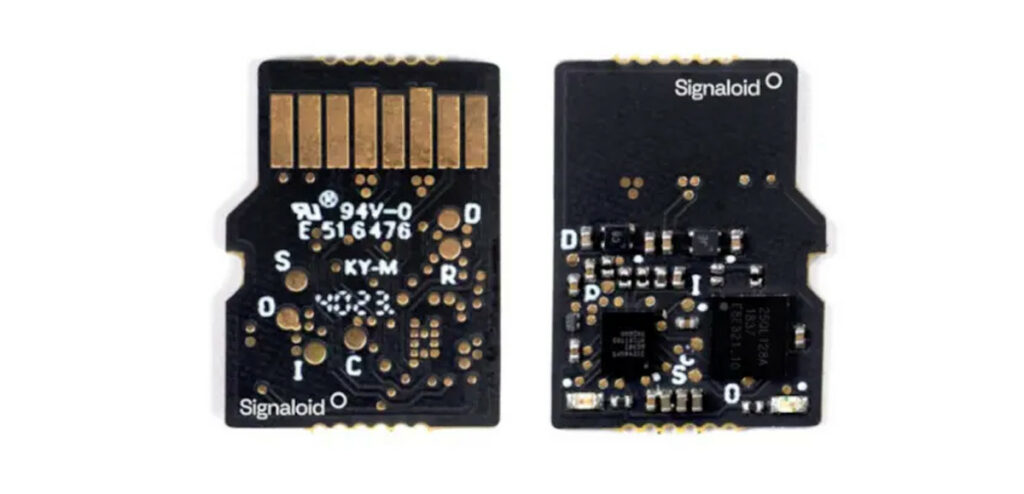
Signaloid’s New FPGA Board Comes in a microSD Form Factor
Signaloid Ltd., a startup specializing in uncertainty processing, has released a unique FPGA development board in the format of a microSD card. Called the Signaloid C0-microSD, the board aims to Simplify FPGA development and offer access to Signaloid's uncertainty analysis...
Continue Reading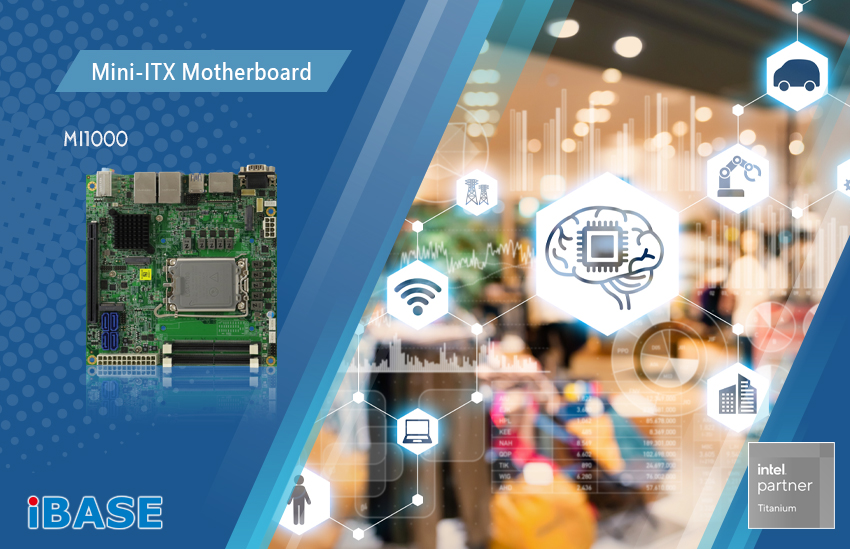
MI1000 Mini-ITX Motherboard Featuring 14th Gen Intel Core Processors and R680E PCH
IBASE Technology Inc., a leading innovator in industrial PC solutions, unveils the MI1000 Mini-ITX motherboard today. Engineered to support the latest 14th/13th/12th Gen Intel® Core™ i9/i7/i5/i3 DT processors (RPL-S Refresh Platform) with up to 65W TDP, these motherboards excel...
Continue Reading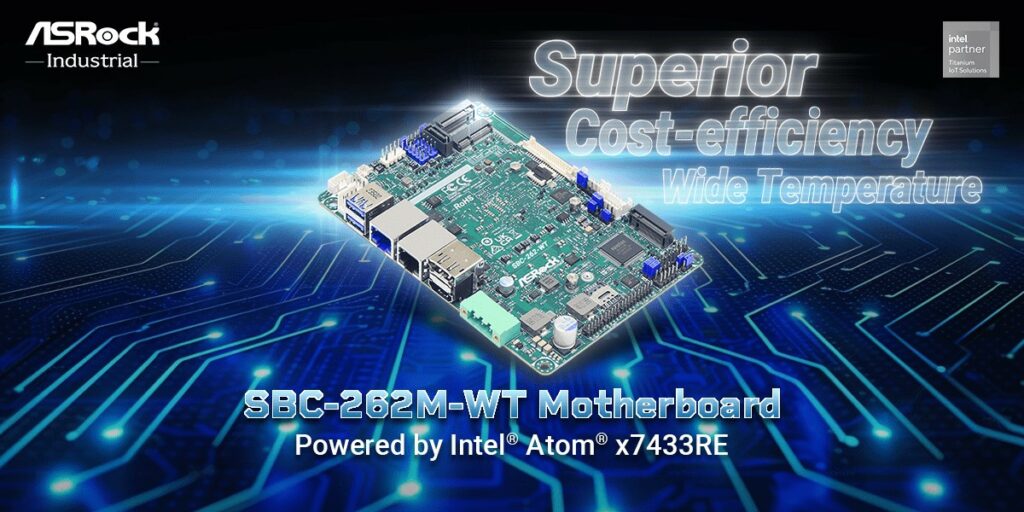
ASRock Industrial Leads with SBC-262M-WT Motherboard Powered by Intel Atom x7433RE for Next-Generation Edge Computing
ASRock Industrial is thrilled to announce the launch of its latest innovation, the SBC-262M-WT 3.5” SBC Motherboard, a new benchmark in edge computing, powered by the advanced Intel® Atom® x7433RE Processor (Amston Lake). Designed with enhanced CPU and GPU performance, this...
Continue Reading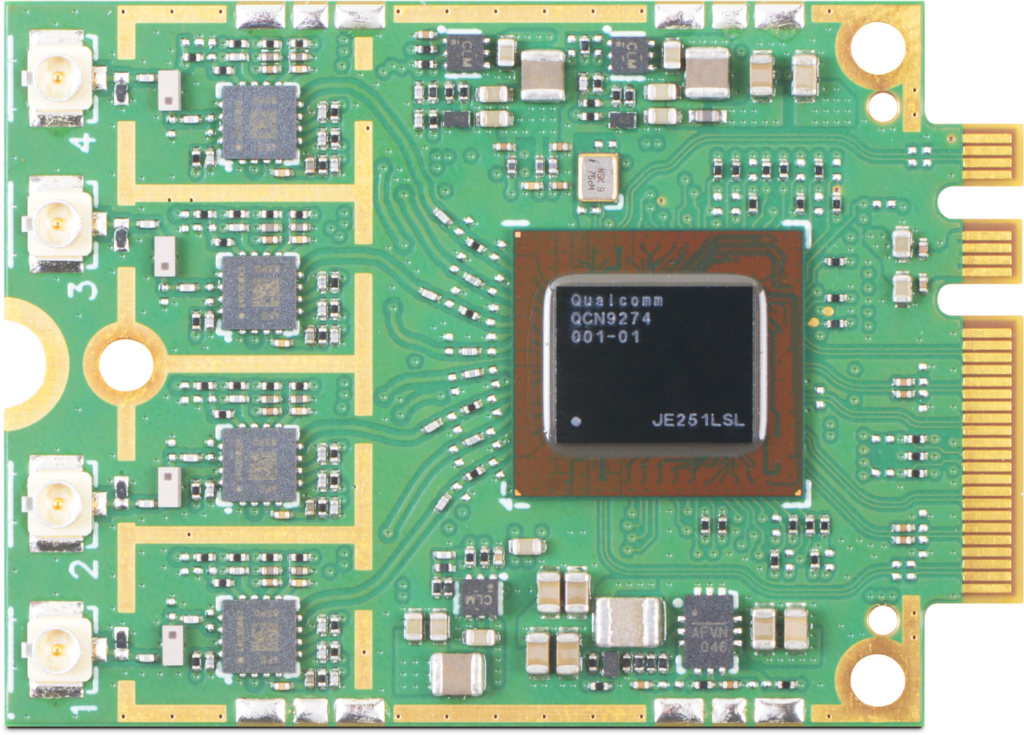
Noni Radio Module: Unlocking WiFi-7 Connectivity with Qualcomm’s Chipsets
The Noni module, powered by Qualcomm’s QCA9274/QCA6274 chipsets, revolutionizes wireless connectivity with advanced WiFi-7 capabilities packed into a versatile M.2 A+E form factor. Tailored for a diverse range of applications, this module thrives in both commercial and industrial...
Continue Reading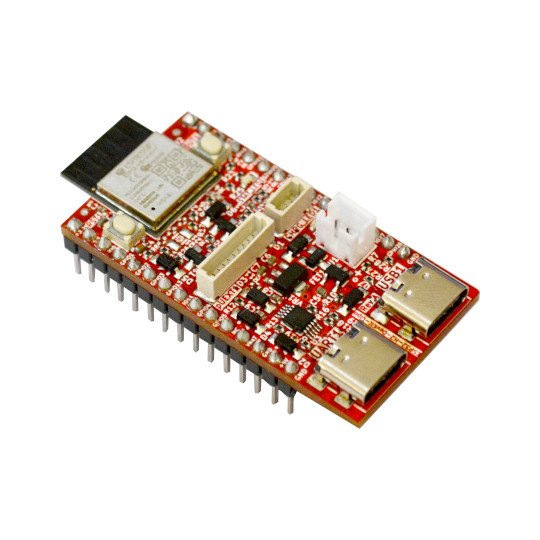
Introducing Olimex’s ESP32-H2-DevKit-LiPo: Empowering IoT Enthusiasts with Affordable Connectivity
Bulgarian open hardware specialist Olimex has revealed its latest innovation, the ESP32-H2-DevKit-LiPo. This compact, cost-effective development board is specifically crafted for individuals keen on delving into Matter devices and the Internet of Things (IoT). At the heart of the...
Continue Reading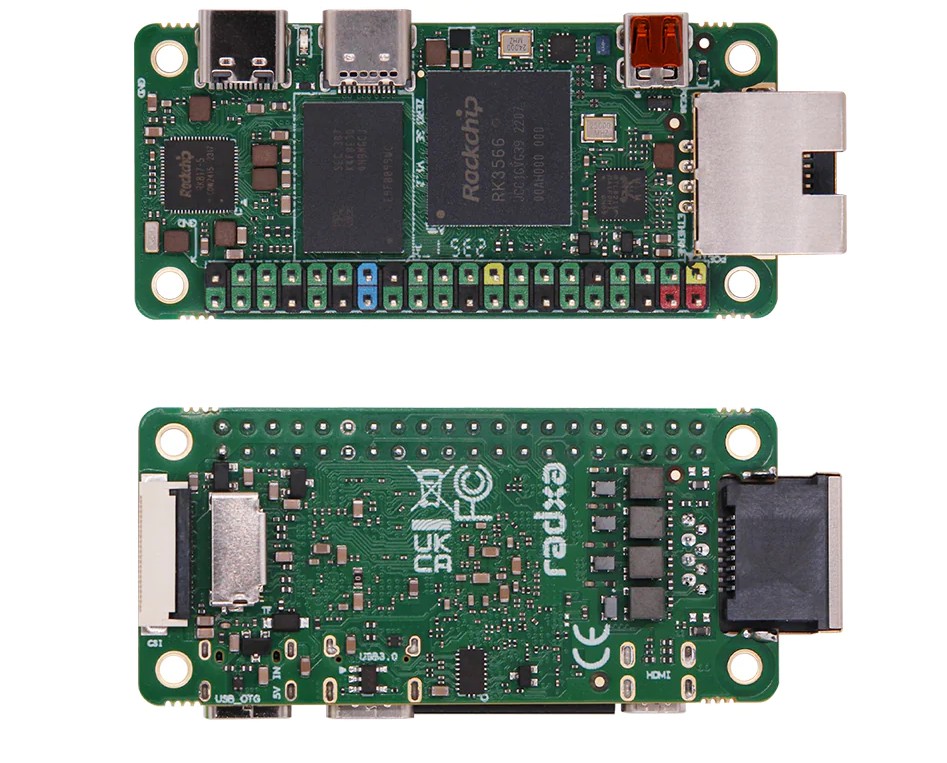
Radxa ZERO 3E SBC is Now Availabe for $15.99
In a previous post, we discussed the Radxa Zero 3W & 3E, both powered by the Rockchip RK3566 and designed to mimic the form factor of the Raspberry Pi Zero 2W and Orange Pi Zero 2W. At that time, Radxa had not disclosed its pricing. However, they have recently announced that these...
Continue Reading