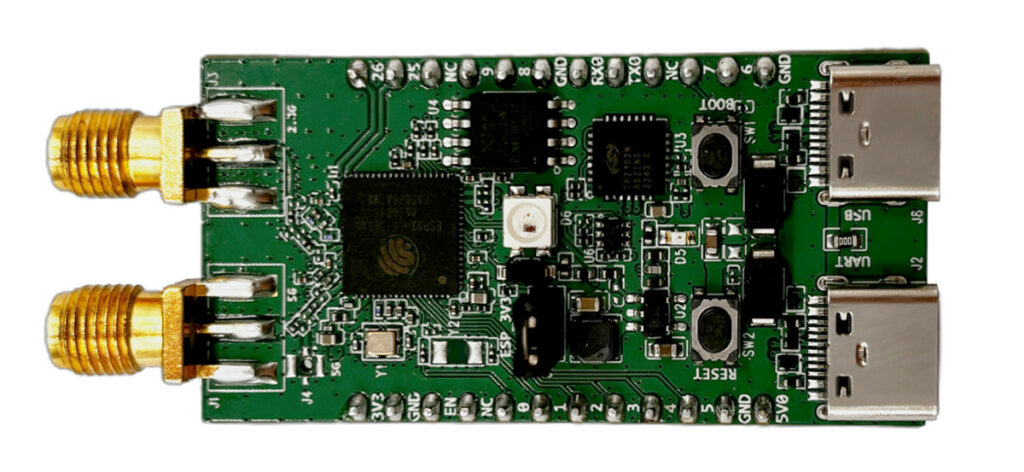
Espressif ESP32-C5 Test Board Features Dual USB-C Port and Dual SMA Connectors
Back in June 2022, Espressif unveiled the ESP32-C5, their first dual-band SoC. But since then we haven't heard any update on that part nor has any development board been showcased, but that changed very recently as they released an official design guide for an ESP32-C5 Test Board. When...
Continue Reading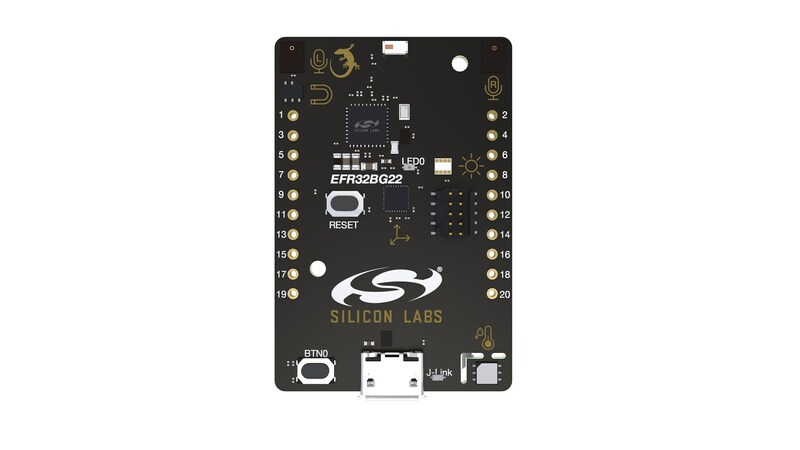
Silicon Labs Streamlines Energy Harvesting Product Development for Battery-Free IoT
Silicon Labs' most energy-efficient Wireless SoC to date with energy harvesting-ready capabilities Silicon Labs, a leader in secure, intelligent wireless technology for a more connected world, today announced their new xG22E family of Wireless SoCs, Silicon Labs' first-ever family...
Continue Reading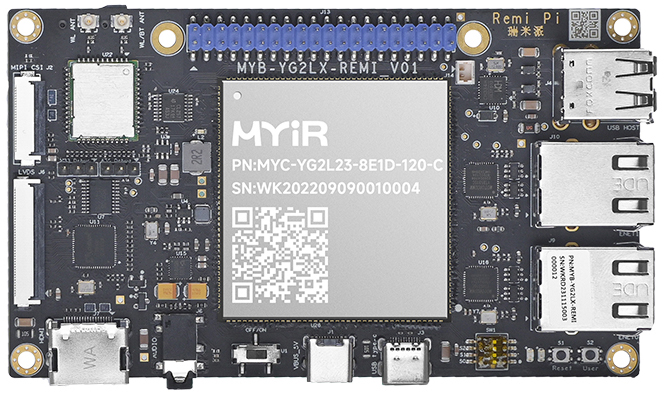
MYIR Remi Pi Features Renesas RZ/G2L SoC and Costs Just $55.00
MYIR Remi Pi is a Renesas RZ/G2L-based SBC, with dual Gigabit Ethernet ports, dual display support, and a MIPI-CSI camera interface. It also features 3D graphics functions powered by Arm Mali-G31. Additionally, it features HDMI, LVDS, and MIPI-CSI for seamless connectivity with various...
Continue Reading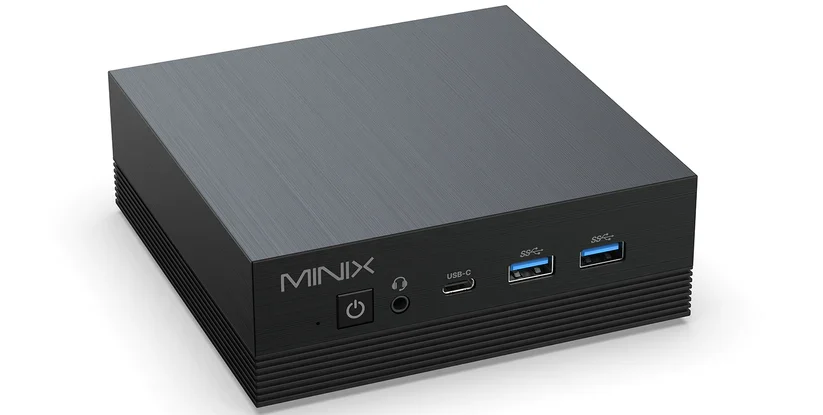
The MINIX Z100-AERO – An Intel N100-Powered Mini PC with 2.5GbE and 1GbE Ethernet Support
The MINIX Z100-AERO is a compact mini PC powered by the Intel N100 CPU, designed to serve efficiently as a router when paired with software like Untangle or OPNsense. This device stands out due to its dual Ethernet ports: a 2.5GbE port managed by the TL8125BG-CG NIC and a 1GbE port...
Continue Reading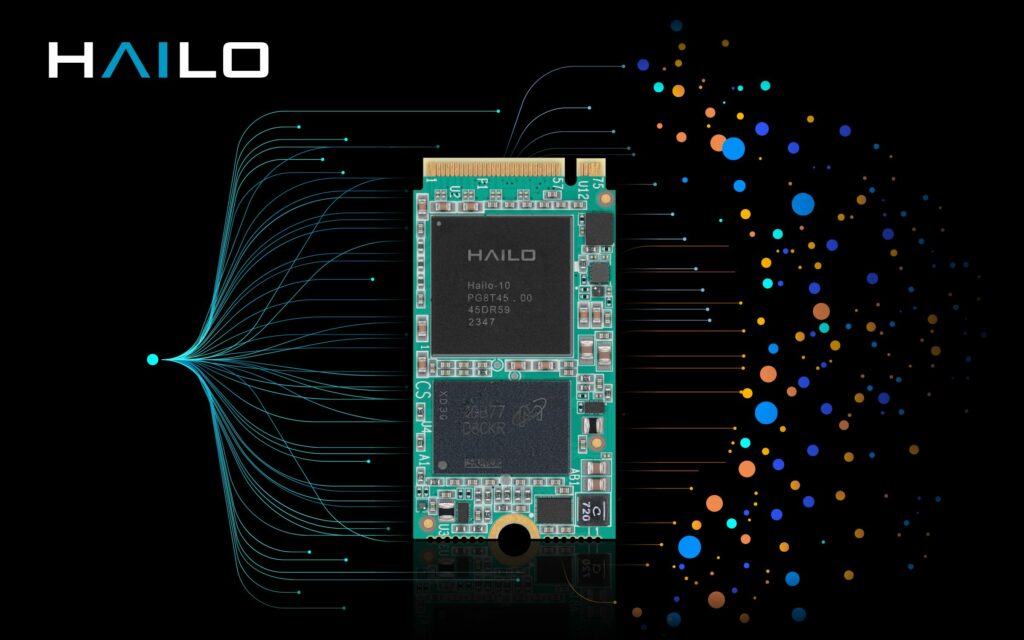
Hailo Closes New $120 Million Funding Round and Debuts Hailo-10, A New Powerful AI Accelerator Bringing Generative AI to Edge Devices
Hailo’s funding now exceeds $340 million as the company introduces its newest AI accelerator specifically designed to process LLMs at low power consumption for the personal computer and automotive industries, bringing generative AI to the edge. Hailo, the pioneering chipmaker of edge...
Continue Reading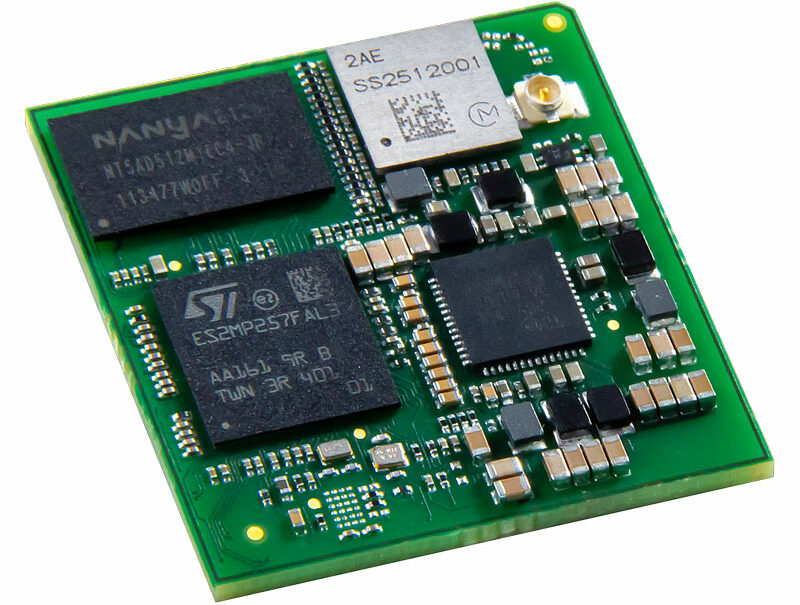
Digi ConnectCore MP25 SoM Features STM32MP25 SoC with 1.35 TOPS NPU in a Tiny Form Factor
At Embedded World 2024, Digi International unveiled the Digi ConnectCore MP25, an ultra-compact System-on-Module (SoM) powered by the STMicroelectronics STM32MP25 SoC. This module is equipped with advanced connectivity features including 802.11ac Wi-Fi 5, Bluetooth 5.2, options for...
Continue Reading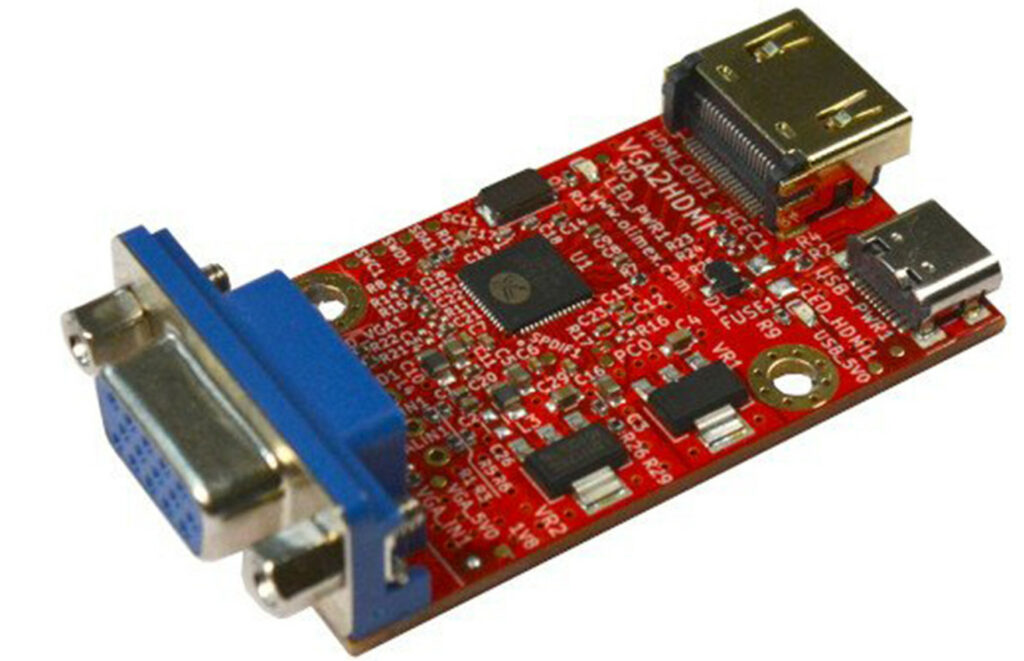
Olimex VGA2HDMI is an Open Source VGA to HDMI Converter Board
Olimex has recently featured a new board named VGA2HDMI It is a VGA to HDMI converter board that can take in VGA signals and convert them into HDMI signals. The reason it's news is because one search will give you many HDMI to VGA converted and not the other way around. The company...
Continue Reading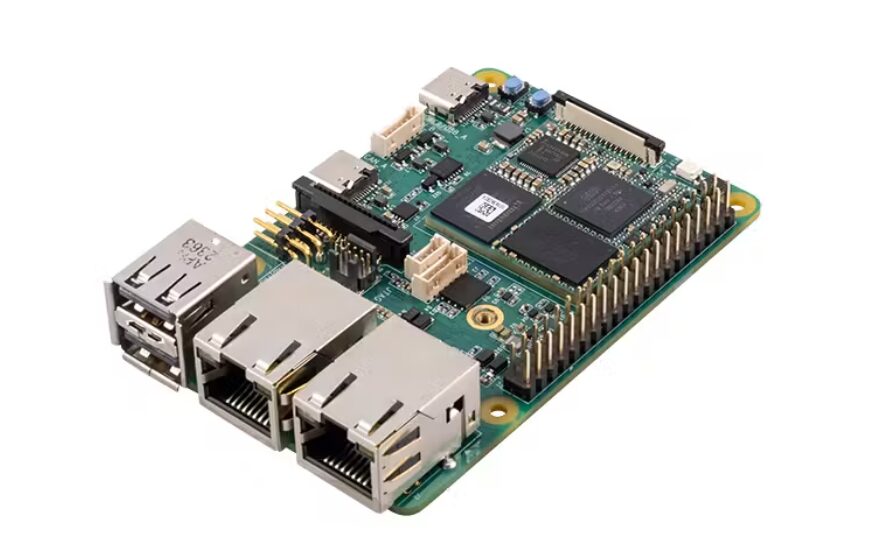
Avnet Unveils MaaXBoard OSM93: A Powerhouse for Edge AI Development
Avnet introduces the MaaXBoard OSM93, a Raspberry Pi-style semi-single-board computer designed to cater to energy-efficient edge artificial intelligence (edge AI) tasks. The board leverages the NXP i.MX 93 system-on-chip (SoC) to power its capabilities, offering a versatile platform for...
Continue Reading