Tag: debug
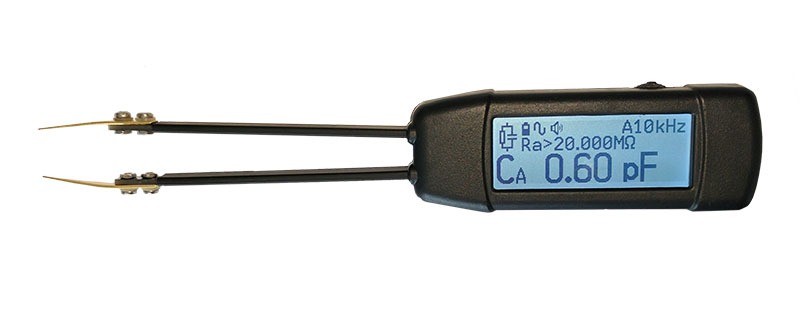
LCR-Reader MP: the Ultimate PCB Debugging Tool
With LCR-, ESR-meter, AC/DC Voltage/Current meter, Oscilloscope and Signal Generator this device covers all needs for low frequency PCB debugging. LCR-Reader-MP recently released by Siborg Systems Inc. which joins the LCR-Reader family of handheld LCR- and ESR-meters, offers users...
Continue Reading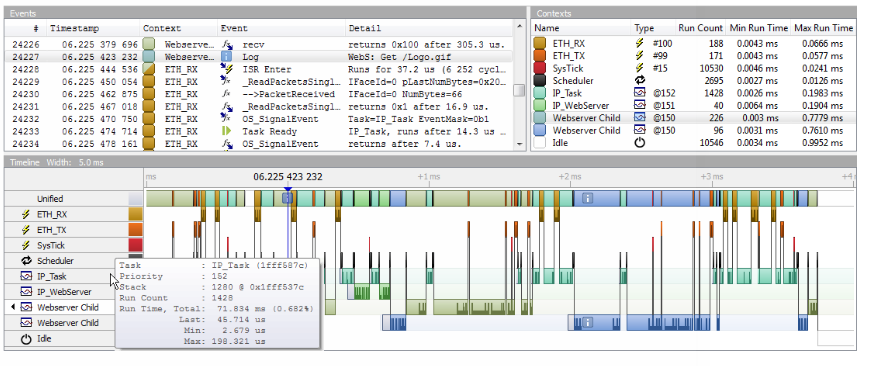
SystemView PRO – Analyze your Firmware Behavior Like a PRO
Segger Microcontroller is known for J-Links device about debugging and programming lots of architectures: ARM, Microchip PIC32 and Renesas RX. Segger provides a lot of other software and hardware tools for debugging and programming purposes; SystemView is one of these tools. SystemView...
Continue Reading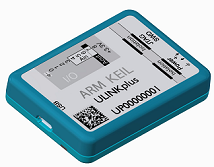
ULINKplus, A Debug Adapter With Power Measurment
While building an ultra-low power application, sensitive hardware and software validation is required to reach system and long battery life. Testing will need an interaction with the tested parts, like simulating input pins of the target application. These difficulties could be solved...
Continue Reading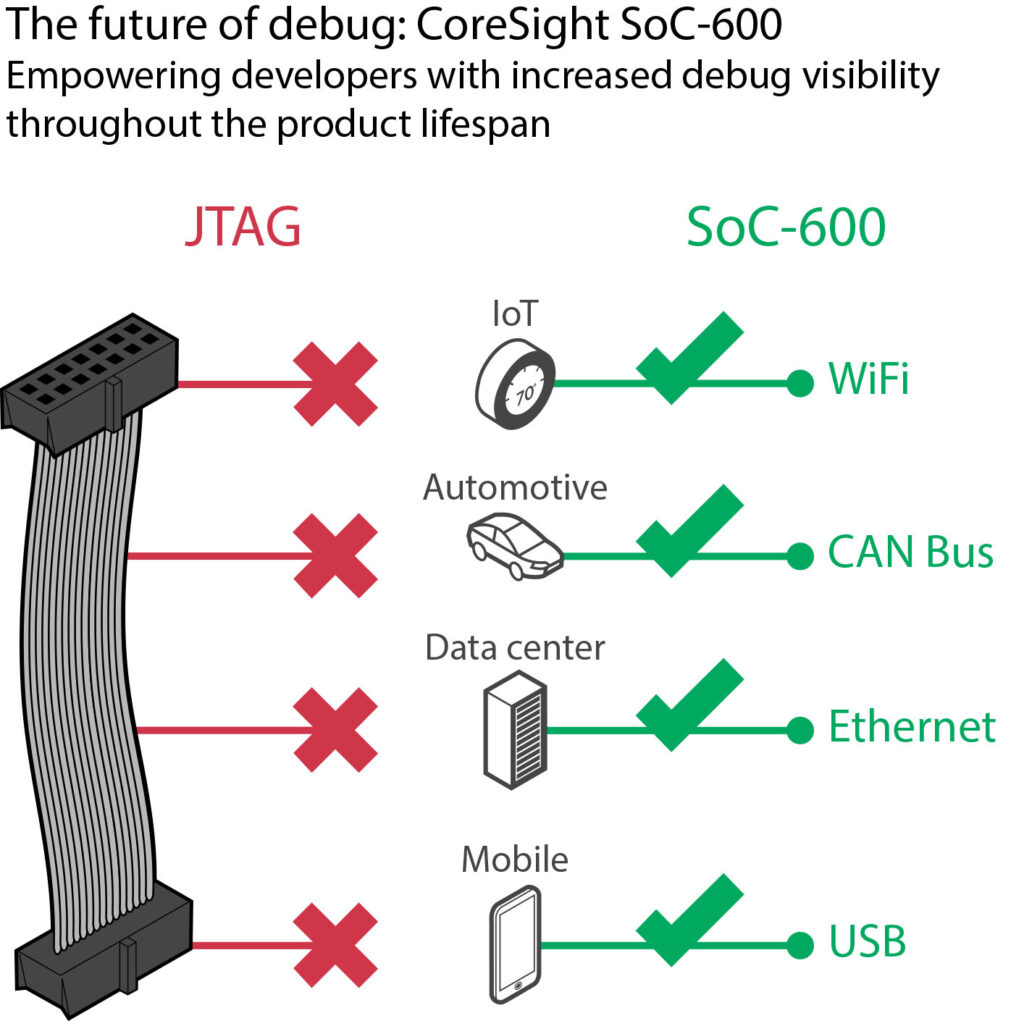
ARM CoreSight SoC-600, The Future of Debug
Debugging is an important part of the design process that is necessary to identify and fix errors. Over the decades, debug tools had evolved providing easier and simpler solutions. Today, ARM introduces CoreSight SoC-600 as the next-generation debug and trace tool that speeds up...
Continue Reading
Issues with printf function
The C library function printf() is one of the common used functions in embedded systems world to debug the code in real time over a serial connection. Using the printf() over serial is under debate and may not be optimal for embedded systems and that’s what Jacob Beningo over EDN tries...
Continue Reading